7 Most Effective Strategies to Minimize Fleet Vehicle Downtime
How to reduce fleet vehicle downtime and keep your business running
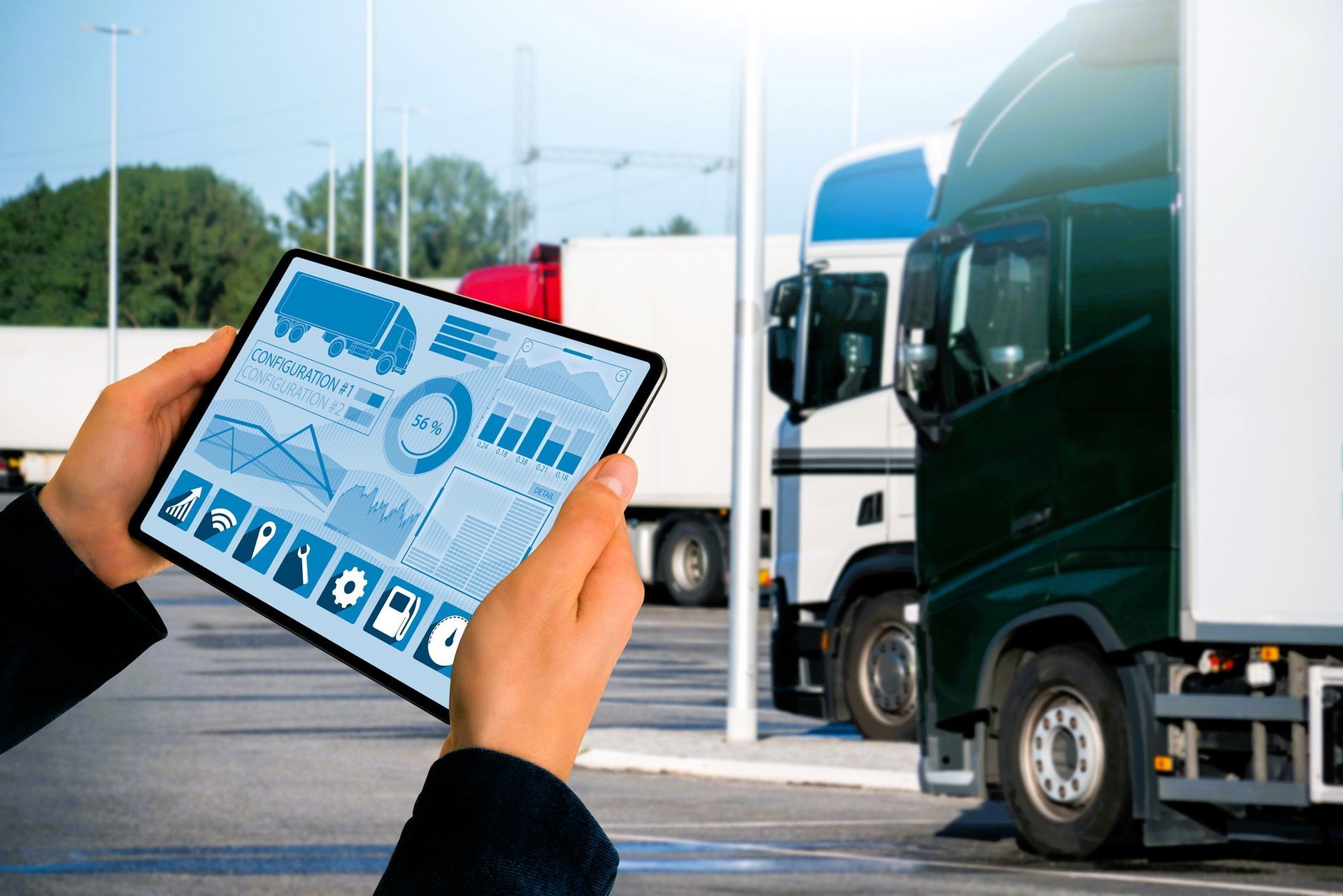
For fleet managers, business owners, and logistics professionals, vehicle downtime isn’t just frustrating—it’s costly. Every minute a truck sits idle, deliveries are delayed, costs pile up, and efficiency takes a hit. It’s the kind of problem that can turn a well-oiled operation into a logistical nightmare.
The good news? While downtime is inevitable at times, it doesn’t have to disrupt your business. With the right approach, you can significantly reduce unexpected breakdowns, keep your fleet moving, and avoid those frustrating moments when a vehicle is out of commission just when you need it most.
Here’s how to take control and minimize fleet vehicle downtime.
1. Routine Inspections: Catch Problems Before They Catch You
Many costly repairs start as small, preventable issues that go unnoticed. A brake pad that’s wearing thin today could mean a total brake failure next month. A tire with low pressure might be fine now, but on the highway, it’s a blowout waiting to happen.
Routine vehicle inspections are the easiest way to catch these problems before they escalate. Many fleet managers require daily or weekly inspections focusing on key areas like tires, brakes, fluids, and lights. Research shows that fleets with structured inspection routines see a noticeable drop in maintenance-related downtime.
The key is consistency. A simple checklist helps ensure no crucial step is skipped.
Make it even easier by ditching paper forms and switching to digital inspection tools. When drivers can log issues in real time and send alerts instantly, you cut down response time and prevent minor problems from becoming major setbacks.
2. Preventive Maintenance: The Fix-It-Before-It-Breaks Approach
A solid preventive maintenance program can save thousands in emergency repairs and lost productivity. Instead of waiting for something to break, schedule regular servicing—oil changes, belt replacements, and system checks—before problems arise.
A well-maintained vehicle runs more efficiently and lasts longer. Something as simple as a regular oil change prevents engine overheating, while replacing brake pads on time keeps an entire brake system from failing.
Following the manufacturer’s maintenance schedule might seem basic, but it’s a game-changer. It’s not just about keeping vehicles in good condition—it’s about avoiding the kind of breakdowns that take trucks off the road for days at a time.
3. Fleet Management Software: Stay One Step Ahead
Trying to track vehicle maintenance manually is like trying to juggle a dozen moving parts—it’s only a matter of time before something gets missed. Fleet management software simplifies everything, automating reminders, tracking service history, and even alerting you to potential issues before they cause a breakdown.
With real-time diagnostics, fleet managers can address small problems before they turn into costly repairs. Companies that use these systems report a major improvement in uptime simply by staying ahead of maintenance schedules instead of reacting to problems as they come.
If you’re still relying on spreadsheets or manual tracking, upgrading to fleet management software could be one of the best decisions you make.
4. Driver Training: Reduce Wear and Tear from the Start
Fleet vehicles don’t just wear out on their own—how they’re driven matters just as much as how they’re maintained.
Harsh braking, rapid acceleration, excessive idling—all of these put unnecessary strain on engines, brakes, and tires, leading to more frequent repairs and unplanned downtime.
The solution? Driver training programs that emphasize fuel-efficient, low-impact driving techniques. Teaching drivers simple habits—like easing into stops rather than slamming on the brakes—can extend the life of key components and reduce maintenance costs by thousands every year.
Plus, drivers who are more aware of how their behavior affects vehicle performance are also more likely to notice and report potential issues before they become serious problems.
5. Choose the Right Vehicles for the Job
Not all fleet vehicles are built the same, and choosing the wrong ones for your needs can lead to constant repairs and higher maintenance costs.
If your fleet operates in stop-and-go traffic, for example, vehicles with durable braking systems should be a priority. If you haul heavy cargo, you’ll need trucks built to handle the weight, or you’ll find yourself dealing with constant transmission failures.
Fleet managers who analyze breakdown data when selecting new vehicles spend less on repairs in the long run. Looking at historical performance, common repair trends, and operating conditions helps prevent costly mistakes when expanding or upgrading the fleet.
6. Streamline Repairs and Build a Reliable Service Network
Even with the best maintenance, breakdowns will happen. The real question is, how quickly can you get vehicles back on the road?
An efficient repair strategy includes:
- Partnering with trusted mechanics who understand your fleet’s specific needs
- Stocking common replacement parts to avoid unnecessary delays
- Using mobile mechanics for on-site repairs instead of towing vehicles to a shop
A strong service network can mean the difference between a quick fix and days of lost revenue. When you have reliable partners in place, vehicles get repaired faster, and downtime is minimized.
7. Use Data to Predict and Prevent Issues
The best fleet managers don’t just react to breakdowns—they prevent them by using fleet data to identify problems before they happen.
Telematics and vehicle tracking systems collect valuable data, including:
- Engine diagnostics and performance trends
- Fuel consumption and efficiency patterns
- Driver behavior that contributes to wear and tear
By analyzing this data, you can predict when a vehicle is likely to need maintenance rather than waiting for something to go wrong. Fleets that actively use telematics to monitor vehicle health and maintenance needs see a significant reduction in unplanned downtime.
If you’re not already leveraging this kind of data, you’re leaving money on the table—and increasing the risk of preventable breakdowns.
Keep Your Fleet Moving
Reducing vehicle downtime isn’t just about cutting costs—it’s about keeping your business running smoothly, meeting customer expectations, and staying ahead of the competition. The fleets that thrive aren’t the ones that wait for problems to arise—they’re the ones that stay ahead of issues, train their drivers, and invest in smart maintenance strategies.
If you’re ready to optimize your fleet and cut down on unnecessary downtime, SLC Fleet Pro Mobile Mechanic is here to help. With expert on-site repair services and fleet maintenance solutions, we make sure your vehicles stay on the road where they belong.
Get in touch today to see how we can help streamline your operations and keep your fleet moving forward.